加速する、セメント産業の廃プラリサイクル
新しい塩素除去技術で「塩ビを含む廃プラスチック類」の有効活用に挑む
セメント製造の代替燃料として、塩ビを含む廃プラスチックを再利用する動きが加速しています。新しい塩素除去技術の開発により、安全、安定的に大量の廃プラスチックが処理できるようになったためで、塩ビリサイクルの選択肢の広がりという点でも見逃せない動き。今回は、業界最先端の設備により着実に実績を重ねつつある宇部興産(株)の苅田(かんだ)セメント工場(福岡県京都郡苅田町長浜町7/Tel 093-434-2111)と、この春から新たな事業をスタートさせる東ソー(株)の南陽事業所(山口県周南市開成町4560/Tel 0834-63-9800)の取り組みを取材しました。
●究極の資源リサイクル工場
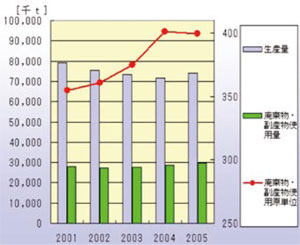 |
セメント生産高と廃棄物・副産物使用量・使用原単位の推移(出典:(財)日本セメント協会) |
セメントの生産量は1996年度の1億トンをピークに減少を続け、2005年度は約7400万トン(前年比103.1%)とやや持ち直したものの、一方では石炭、重油など燃料コストの高騰もあって、業界を取り巻く環境は依然厳しい状況が続いています。
こうした中、近年の廃棄物問題、資源・エネルギー問題の高まりを背景に、「究極の資源リサイクル工場」としてセメント産業の役割を評価する声が強まっています。
石灰石や粘土、硅石、鉄精鉱などを1500℃近い高温で長時間焼成するセメント製造設備は、(1)ダイオキシンなどの有害物が分解される、(2)セメント原料と同じ成分を含む多様な代替品を原料に取り込むことができる、(3)廃棄物を無害化し安全かつ安定的に大量処理が可能、などのことから、もともと廃棄物処理に適したプラントであり、廃タイヤなどを燃料に利用する試みは既に1980年代から始まっていました。
セメント産業への注目の高まりはこうした技術の蓄積を背景としたもので、業界にとっても循環型社会への貢献と同時に製造コスト削減の効果が見込めることから、現在各メーカーとも「2010年までにセメント1トン当たり400sの廃棄物利用」という業界目標の達成へ向けて取り組みを強化し、業界平均では2004年にその目標を達成していますが、各社とも更なる利用率向上に努めています。
セメント工場でリサイクルされる廃棄物は、原料の代替となるもの(原料系)と燃料の代替となるもの(燃料系)の2つに分けられますが、数量的には原料系のほうが圧倒的多く、燃料系の利用促進が今後の課題となっています。その中で補助燃料として期待を集めているのが塩ビを含む廃プラスチック類。ただ、塩ビなど塩素を多く含むものを燃やすと、キルン(セメントを焼成する高熱炉)内の塩素濃度が上昇して製品の品質やプラントの安定操業に影響するため、それに対応した塩素除去技術が欠かせません。今回取り上げた2社の事例は、そうした新しい技術開発により、これまでは困難だった高濃度塩素廃棄物の再利用に挑むモデルケースのひとつといえます。
ケース1
宇部興産(株)苅田工場の高濃度塩素バイパス設備
国内最大の塩素除去技術で年間6万トンの廃プラスチックを代替燃料に再利用
●大量の塩素を無害化処理
化学を中心に建材、機械、金属成形など多彩な事業を展開する宇部興産は、セメント製造の分野でもトップ企業のひとつです。事業は1923年から始まっており、現在は山口県美祢市と宇部市、福岡県苅田町にある3つの工場を拠点に年間800万トンのセメントを製造しています。
その中で最も強力に廃棄物リサイクルを推進しているのが、年間約200万トンのセメントを生産する苅田工場。同工場では廃棄物利用の業界目標値を既に2004年度で達成しており、2006年度は1トン当たり463sとさらに上回ることが見込まれています。
苅田工場が扱う廃棄物の種類は、原料系では粘土と成分の近い石炭灰や建設発生土、自治体から出る都市ごみ焼却灰、高炉スラグなどの鉄鋼副産物、汚泥類、肉骨粉など。燃料系では廃プラスチック類、廃油類のほか、RDFなども利用されています。
冒頭に記したとおり、セメント工場でリサイクルされる廃棄物は原料系が中心で、苅田工場の場合も燃料系は1トン当たり28s程度となっています。また、燃料系の6割は廃プラスチック類が占めています。即ち、年間約3万4千トンの廃プラスチックを苅田工場がリサイクルしている勘定です。
こうした実績を可能にしているのが、2005年4月に設置された業界最大規模の高塩素バイパス設備。キルン内に発生する塩素を大量に除去、無害化して系外に排出するこの設備の導入により、苅田工場では廃プラスチック類ばかりでなく、都市ごみ焼却灰や汚泥類といった塩素を多く含む原料系廃棄物もより有効に再利用することが可能となりました。
「塩素バイパスという技術自体は当社が初めてではなく、各社10年以上前から既に実用化している。しかし、従来の技術は低濃度の塩素しか処理できず、廃プラスチックなど塩素分の多い廃棄物を積極的にリサイクルしていく上では能力が小さすぎることから高塩素バイパス設備の開発に取り組んだ。業界初の技術だっただけにプロセスの決定までいろいろ苦労したが、現在は順調に連続運転を行っている」(苅田工場・松岡守副工場長)
昨年の「第15回地球環境大賞」(主催=フジサンケイグループ)では、高塩素バイパス設備の開発に対してフジサンケイグループ賞が贈られています。
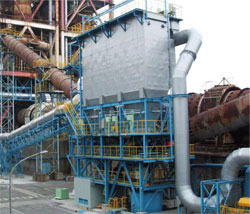 |
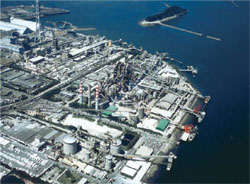 |
苅田工場の高塩素バイパス設備 |
苅田工場全景 |
●重要性増す、廃プラの役割
苅田工場の高塩素バイパス設備は、キルン入口に接続した予熱搭と呼ばれる装置の下部に連結しています(下図参照)。セメントの製造工程でガス中の塩素濃度が高くなるのがこの部分で、ここから抜き取られたガスおよびダスト類をバグフィルターで捕集、洗浄、脱水した後、廃水を無害化処理して系外に排出する一方、残ったダスト類は再びセメントの製造工程に戻され原料の一部に利用されます。
高塩素バイパス設備が国内最大とされる理由は、そのガスを抜き取る能力(抽気率)の大きさにあります。従来の技術では1〜3%に留まっていた抽気率を一挙に10%まで引き上げることに成功したことで、塩ビを含む廃プラスチック類など高塩素廃棄物の許容範囲は大きく広がりました。
「高塩素バイパス設備のおかげで余力ができたということ。塩素がいくらあってもいいとは言わないが、塩素濃度5%程度のものでも問題なく処理できる力がついた。当工場に入ってくる廃プラスチック類は建設系の混合廃プラが中心で、紙などの雑多な異物も含む処理しにくいものだが、代替燃料としてのその役割は、熱量面、コスト削減面でともに大きくなってきている。それだけに、高塩素バイパス設備を安定運転に結びつけ、大きな課題だった塩素の問題をクリアできたことの意味は大きい。我々としてはこれに満足することなく、今後とも処理の難しい廃棄物にあわせた技術や設備を幅広く用意して、さらなる廃棄物処理事業の展開に取り組んでいきたい」(松岡副工場長)
苅田工場が1年間に使用する石炭の量は約22万トン。現在その20%を燃料系廃棄物で代替していますが、同工場では「50%以上、約12万トン」を目標に事業を進めていく計画です。
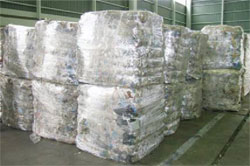 |
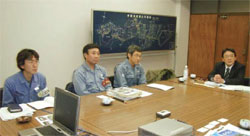 |
苅田工場に搬入された廃プラスチック類 |
苅田工場の関係者の皆さん。
左から2人目が松岡副工場長 |
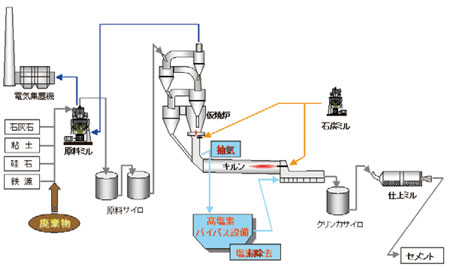 |
高塩素バイパス設備フローシート |
ケース2
東ソー(株)南陽事業所のクロルバイパス設備
廃プラスチック類の受入開始に備え設備を増強。
年1万5000トン処理計画
●6月から本格稼動へ
苛性ソーダや塩ビモノマーなどを主力とする総合化学メーカーの東ソー。そのセメント事業を担う南陽事業所は山口県周南市(旧新南陽市)の周南コンビナートの一画にあります。
同社がセメント事業を開始したのは1953年のこと。現在の生産能力は年間290万トンで、業界の中では中規模メーカーに位置づけられますが、もともと南陽事業所の化学工場から発生する廃棄物・副産物を自社処理することを主目的にスタートしたという経緯があり、それだけにプラントの操業当初から廃棄物の有効利用では積極的な取り組みを続けてきました。その後コンビナート内の他企業など外部からの受け入れも行うようになり、現在では年間約50万トンの廃棄物・副産物をリサイクルしています。
その種類は、原料系としては、社内の石炭自家発電設備から出る石炭灰20万トンのほか鉱滓、汚泥などが中心。燃料系ではで廃タイヤ、肉骨粉などのほか、周南市の家庭ごみから製造したRDFも年間約5000トン受け入れており、自治体の廃棄物・環境行政への寄与という点で地元からも高い評価が寄せられています。
同事業所では、セメント1トン当たり約400sという廃棄物利用の業界目標は未だクリアできていませんが、原料系廃棄物の利用はほぼ頭打ちの状態で、今後利用率を高めていく上ではこれまで受け入れてこなかった廃プラスチック類を含め、燃料系廃棄物の利用を増やしていくことが大きな課題。そこで考えられたのがクロルバイパス設備の設置計画です。
「家庭ごみのRDFも結構塩素の量は多いが、その程度なら現在のプラントでも問題ないように設計されている。しかし塩ビを含む廃プラスチックなどの処理を進めていくためには、クロルバイパスでいったん系外にガスを抜き出して処理することがどうしても欠かせない。クロルバイパスがあれば中間処理業者の段階で塩ビを分別するような手間をかけずに済むし、塩素濃度の高い廃棄物をもっと利用できるようになれば、さらなる資源の有効活用にも貢献できる」(東ソーセメント事業室の佐藤正勝室長)。
同事業所のクロルバイパス設備は、5月までに試運転を終了し、6月から本格稼動に入る予定で、現在その作業が順調に進められています。
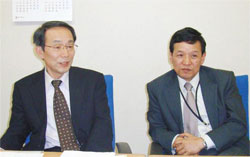 |
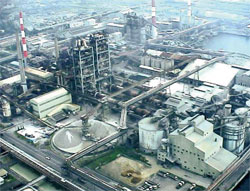 |
セメント事業室の佐藤室長(右)と田村次長 |
南陽事業所のセメントプラント |
●「塩ビの積極的受け入れ」で独自色
クロルバイパス設備の仕組みはつぎのとおり。予熱塔(図ではSP塔)の下部からガスとダストを抜き取り冷却した後、洗浄工程で塩素分を水洗いして廃水を系外に排出する一方、残ったダストは原料工程に戻して再利用することとなります。
南陽事業所では当面、塩素濃度5%程度の廃プラスチック類を年1万5000トン処理していく計画。また、廃プラスチック類の処理に備えて、キルンに廃プラスチックを吹き込むための専用の破砕機も新設される予定です。
同事業所の独自性は、塩ビの受け入れということに関してより意欲的な姿勢を見せている点にあります。
「廃プラスチック類は製紙や鉄鋼メーカーでも燃料への代替を進めているし、一方で中国への輸出もあって、奪い合いに近い状態になりつつある。実際セメント業界全体で使っている廃プラスチック類は年30万トン程度でここ数年頭打ちの状態にあり、そうなると塩素が少し多めに入っていても引き受けられるほうが有利になる。
同事業所で扱う廃プラスチックは建設系の廃材が中心になると思うが、クロルバイパスが稼動すれば塩ビが仮に10%以上入っていても、量的には制限されるが、引き受けることができるようになる。我々は廃プラスチックの受け入れという点では業界でも最後発の組に入るが、最後発だからこそ、そのことを最大の謳い文句にしたい」(佐藤正勝室長)。
●まずは石炭の1割を代替
最後に、代替燃料としての廃プラスチックの役割について、東ソーでは次のように説明しています。
「セメント業界はいま生産量こそピーク時の7割程度まで下がっているが、どのメーカーも元気が出てきている。それは廃棄物の処理事業が順調にいっているせいだ。特に、石炭の値段が上昇傾向にある中で、廃プラスチック類を燃料に代替する意味は大きい。当社としては最低でも石炭の1割は廃プラスチック類で代替していきたい」(セメント事業室の田村英一次長)。
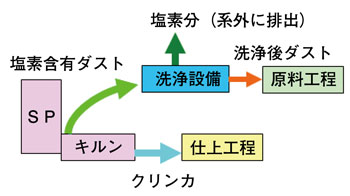 |
クロルバイパス設備の処理フロー |
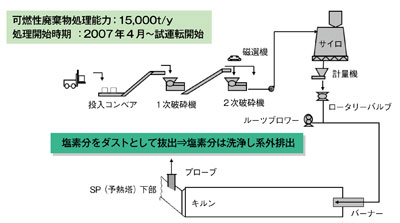 |
破砕工程の処理フロー |
|