東芝の「塩化ビニル混入廃プラスチック油化装置」
「塩ビ混入率最大50%」まで処理可能、5年間の研究成果が実用段階に
|
(株)東芝(本社=東京都港区芝浦1−1−1、TEL.03−3457−4398)は、塩ビなどの塩素系プラスチックが、最大50%まで混入した廃プラスチックを油化できる装置の実用化に成功、昨年11月から営業展開に入っています。容器包装リサイクル法への対応を間近に控え、塩ビ廃棄物処理問題に大きなインパクトを与えるこの最新システムの実態を、同社京浜事業所の入舟工場(横浜市鶴見区)に取材しました。 |
|
■ 塩ビを分別することなく安全に処理
|
東芝では、自社工場から出る廃プラの有効利用と廃棄物問題への対応などを踏まえて、およそ5年前(平成4年)から廃プラ油化技術の開発に取り組んできました。
同社の開発方針は、当初から「塩ビ混入率最大50%」までの産廃系廃プラ処理を目指してきた点に大きな特徴があり、同じ油化技術でも、塩ビの割合が低い(8〜12%程度)一般都市ごみの処理を対象とすることが多い他のメーカーとは一線を画す内容となっています。
「塩ビユーザーや塩ビ排出量の多い企業、あるいは地域の特殊事情で塩ビ混入率の高い廃プラを処理しなければならない自治体などで、塩ビを分別することなく安全に処理できるシステムを作ることが重点課題だった」と、同社環境システム部の浅野隆一部長が説明するように、塩ビ廃棄物の処理により重点を置いた東芝の開発動向は、塩ビ業界の関係者にとってもここ数年大きな関心の的になっていました。 |
■ 24時間連続運転で稼働率も向上
|
平成6年8月にはバッチ式の実証プラントを用いて試運転も開始されていますが(本誌No.12/平成7年3月号)、今回開発された油化装置はその最初のモデルから数えて3世代目に当たるもので、試行錯誤を積み重ねた結果、技術面で様々な改良が加えられています。
中でも、最大の違いは不連続運転のバッチシステムから24時間連続運転が可能なシステムに変更されたことで、これにより、「装置の起動、停止のたびに昇温降温を繰り返すためランニングコストが嵩み不便な点も多い」(浅野部長)バッチシステムに比べて、装置の稼働率と使い勝手が大幅に向上することとなりました。
また、油の分解方法も当初から常圧熱分解方式が採用されており、操作性とメンテナンスの作業が容易になったことも、新システムの特長のひとつと言えます。
なお、入舟工場では現在、処理量500?/日規模の実証プラントが運転されていますが、実際の商品は、処理量5トン/日〜最大30トン/日までのパイロットシリーズが用意されています。 |
■ 廃プラ1トン(塩ビ50%)が470kgの油に
|
|
システムの処理フローは、図に示したとおり脱塩酸工程〜油生成工程まで6つの工程から成り立っています。まず、10mm角程度に破砕した廃プラを270℃〜300℃に加温し、脱塩素装置で97%以上の塩化水素ガスを分離した後(脱塩酸工程)、分解槽で温度を400〜450℃に上げて油成分をガス化し(分解工程)、最後に生成油回収塔において重油、軽油、灯油の3種類に分けて油を回収する(油生成工程)というのが基本ライン。
一方、脱塩酸工程で発生した塩化水素ガスは吸収塔に導かれ、水道水との接触により35%の濃塩酸として回収されるほか(塩素処理工程)、分解工程で排出される残渣は熱したセラミックボールを回転させて粉末化する東芝独自の技術で処理され(残渣処理工程)、石炭と同程度の熱量をもつ固形燃料として利用することも可能です。
また、排ガス処理工程では、スクラバーとバーナーの組み合わせで、生成油回収塔で回収し切れなかった低沸点のガス成分等を含め完全な排ガス処理が行われます。
以上の工程を通じて、生成される油は廃プラ1トン当たり塩ビ混入率50%で470kg、10%の場合810kgで、さらに塩酸も回収され再利用されることとなります。
|
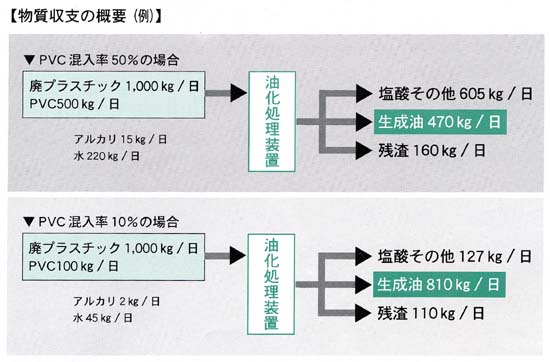
■ システムの要は脱塩酸技術
|
|
環境システムエンジニアリング部の伊部英紀課長によれば、「全工程の中で最も苦心したのが脱塩酸処理の工程だった」だと言います。「塩ビの混ざった廃プラの場合、脱塩酸すると粘性が高まり運搬、加熱の調整が難しくなる。調整を誤るとプラスチックが装置の壁面に溶着するし、温度を上げ過ぎると分解が早まる。これはスクリューフィーダーによる加熱と、適切な温度制御によって解決している」。
スクリューフィーダーとは、加熱した廃プラを水平均等に押し出すことのできる装置で、これにより塩化水素ガスをシステムの外に漏らさず脱塩素装置内で97%まで分離することが可能になりました。 |
■ 固形燃料化にも脱塩酸技術を利用
|
|
東芝では現在、この脱塩酸技術だけを分離して新たな事業を展開する計画も進められています。
「塩ビ混入廃プラの油化は50%までが限界であり、もともと石油使用割合の低い塩ビがそれ以上多くなると回収できる油の量が少なくなって採算が合わない。従って、70〜80%といった塩ビ混入率の高い廃プラを、脱塩酸技術を利用して固形燃料化するのも有効な方法だと思う。我々は何が何でも油化に拘っているわけではない」と語るのは環境システムエンジニアリング部の渡部攻担当部長。
同社では既に農水省の外郭団体である生研機構(生物系特定産業技術研究推進機構)を通じて農業用塩ビ等の油化処理システムの開発試験に取り組んでおり、来年度一杯でスタンダードタイプの処理装置の開発を終了する予定。この装置が完成すれば、農業用塩ビ等の処理(油化・固形燃料化など)を進める上で有力な切り札になるものと考えられます。
このほか、最近話題となっている高炉への廃プラのコークス代替利用についても、「将来的には鉄鋼メーカーも塩ビ混入廃プラをコークスの代わりに処理していく方向にあると予想される。そうなると日量50トン〜100トンという大量処理に適した脱塩酸装置が必要になるし、実際そういう要望も出はじめている」(渡部部長)とのことで、塩ビ業界としてはこの点でも同社の取り組みに期待したいところです。 |
|